What is Engine Hung Start?
- Isha Federick
- Aug 4, 2018
- 5 min read
What is Engine Hung Start?
The "hung" start happens when an engine is accelerating towards idle RPM, with normal combustion, and an extraction of bleed air occurs. So, the engine never reaches idle RPM but instead keeps running in a lower stage.
Question is, does it respond anyway to throttle movement?
So the answer should be yes, because A hung start happens if the engine stops accelerating towards the idle RPM or "rolls" back after reaching idle. The only correct action in this case is to shutdown the engine! Never advance the throttles in this case. As the airflow through the engine is too low you can easily overshoot the max. EGT (hot start)by introducing more fuel which it depending on the time of the EGT.
The Start System Each engine is fitted with an air starter motor, when engine start is selected, each starter motor will be supplied with air from either the APU, The ground start unit or engine which is already running and capable of supplying air.
APU - the aircraft's normal bleed air system ducting is utilised to pass the air to the starter motor. Non return valves prevent leaking back into the engine compressor during engine start..
The hung start
The EGT being higher than would be expected for the RPM at which the engine has stabilized
The RPM being lower than the engines self sustaining speed
The usual cause of a hung start is insufficient airflow to support efficient combustion and there could a number of reasons for this. For instance at a high altitude airfield, starting an engine which has a contaminated compressor Or, insufficient motive power being applied to the starter motor will prevent the compressor pushing required amount of air through the engine.
A hot start is when the EGT exceeds the safe limit. Hot starts are caused by too much fuel entering the combustion chamber, or insufficient turbine r.p.m. Any time an engine has a hot start, refer to the AFM, POH, or an appropriate maintenance manual for inspection requirements.
If the engine fails to accelerate to the proper speed after ignition or does not accelerate to idle r.p.m., a hung start has occurred. A hung start, may also be called a false start. A hung start may be caused by an insufficient starting power source or fuel control malfunction.
Engine Start
The process of the engine starting follows this basic formula
**Through the opening of bleed air valves, bleed air is sent to an air turbine starter. These devices typically use the high pressure bleed air to spin and engage a centrifugal clutch connected to the engines accessory drive. This in turn causes the N2 shaft within the engine to spin.
**With the N2 shaft spinning, the N2 compressor and the N2 turbines are spinning. This begins to force air through the engine from front to back.
**With the accessory shaft and N2 shafts spinning, accessories should start working and this can be verified by oil pressure indications on the EICAS.
**With increased N2 rotation, ignition will be turned on. These igniters are located in the hot section of the engine and produce small sparks. There should be an indication on the EICAS that the ignition is active.
**With further increase in N2 rotation, fuel flow will be introduced. This will be verified on the EICAS. Once fuel flow is noted, it is important that the next stop happen fairly soon.
**Light off! The fuel is lit by the ignition and now the fire burning in the hot section supplied by air from the compressor is producing thrust across the N2 and N1 turbines.
**As the engine is producing thrust across on the N1 turbine, the N1 shaft is spinning the N1 fan and the EICAS will note this increase in N1 rotation. N1 and N2 rotation speeds increase.
**Above a N2 threshold, bleed air valves supplying the the air turbine starter will close and the starter disengage. The igniters will turn off at some N2 threshold.
**The engine will settle into a stable idle thrust setting.
What can go wrong?
1)Hung start
-N2 fails to spin up sufficiently for fuel flow to be introduced. -Each start has a time limit and the start will be aborted.
2)No ignitors
-Abort the start and switch igniters. -Give MX a call.
3) Failure to ignite
-Fuel flow is introduced but light off has not occurred in a proper timeframe -Fuel is building up in the engine and if light off does occur, it can be damaging. -The start is aborted and dry motoring is performed to clear the engine.
4)ITT exceedence
-There is usually a limitation in the inter-turbine temperature during engine start. -If this is exceeded the start must be aborted -This may require coordination with MX before another start is attempted.
5)The air turbine starter fails to disengage
-This must be corrected before departing -In some engines, MX can correct this with the engine running.
6) The bleed air shutoff valve supplying the air turbine starter fails to close
-This may require an engine shutdown to remedy -However, in some airplanes, this valve can be manually shut by MX with the engine running -Coordination with MX required.
7) Runaway N1 or N2
- If the FADEC isn't managing fuel flow properly, the engine may not settle but continue to spin up. - Abort the start. Coordinate with MX before attempting a restart.
What about starting the engine in the air?
If the engine suffers a flame out, an airborne restart may be attempted. These starts typically happen one of a few ways:
1) Cross-bleed start
2) APU start
3) Windmilling start
The APU start is essentially the same process as above. The crossbleed start, which can also be done on the ground, merely substitutes a running engine at a high power setting to provide the bleed air for starting and is otherwise the same as above.
The interesting start is the windmilling start. The necessity for this means something bad has happened. To need a windmilling start, this means that there are no bleed air sources to supply the air turbine starter. This can mean that all engines are out and the APU is unavailable (BAD!), or merely that bleed valves to a shutdown engine have failed closed and are unable to be opened.
For the EMB-145 that I am familiar with, a windmilling start required descending at an airspeed between 260 KIAS and 320 KIAS and could not be attempted above FL250. In short, you hope that the mass flow through the engine is enough to spin the N2 compressor as the ATS would. With an N2 indication within the engines airstart envelope, you introduce spark and fuel and hope that the engine lights. In the worst case, if you too slow and unable to provide enough airflow prior to light off, the engine can quickly overtemp and be damaged. For this reason it is especially important to abort this kind of start as soon as an abnormality is detected.
**NOTE For good understanding, watch video on the link below,
https://www.youtube.com/watch?v=kZBs344kpkQ
Source: FAA
https://www.faa.gov/…/design.../e…/.../engine_malf_famil.doc
https://www.icao.int/…/caaf2…/Documents/CAAF-09_IP012_en.pdf
Prepared by: Air. Net Team
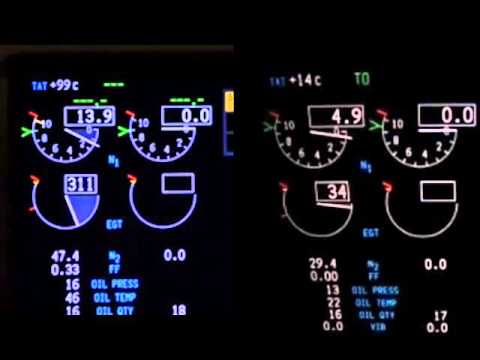

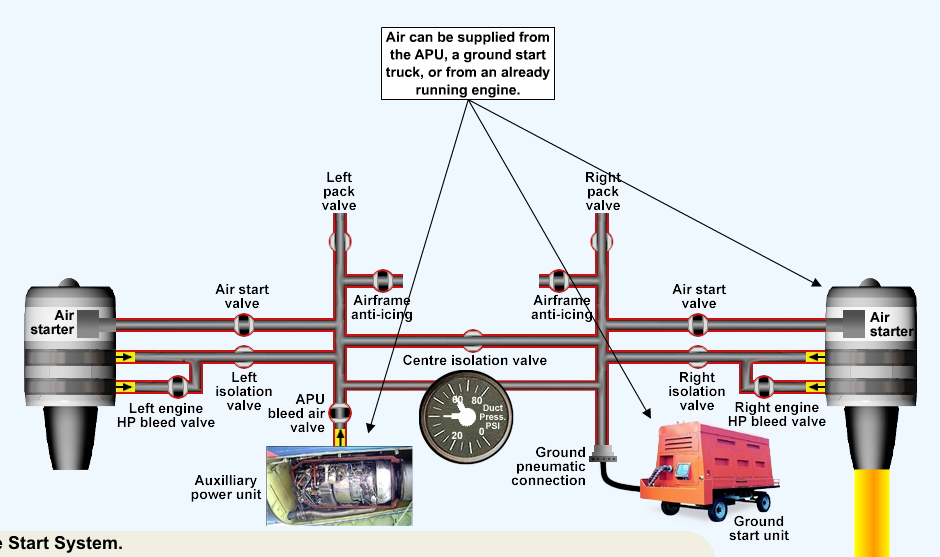
Comments